Celazole® T-Series
PBI PAEK Polymer Compound – Superior polymer durability for your high performance thermoplastic needs
Celazole® T-Series products are PBI compounds designed for injection molding and extrusion. Combining the superior mechanical properties and thermal resistance of PBI with the melt process ability of polyaryletherketones (PEEK or PEKK), these products offer cost-effective high performance. These products are available in pellet form.
Celazole® PBI (polybenzimidazole) is a unique and highly stable heterocyclic polymer. PBI polymers are characterized by high thermal stability; exhibit high strength, broad chemical resistance and unique compatibility with certain other polymers including the polyaryletherketone family.
Celazole® T-Series Explained
T-Series products are composites of Celazole® PBI and polyarlyetherketones and come in formulations designed for some of the most demanding industrial, chemical, petrochemical and semiconductor applications imagined. At the heart of the Celazole® T-Series compound is Polybenzimidazole (PBI) – the world’s highest performing thermoplastic; a highly stable linear heterocyclic polymer known for its exceptionally high (427ºC) glass transition temperature, high strength, thermal stability and broad chemical resistance.
Tractability for injection molding and extrusion is obtained by compounding the PBI with polyetheretherketone (PEEK). Independently, PEEK is a high performance thermoplastic with excellent mechanical properties, chemical resistance and thermal stability, but when compounded with PBI, certain performance advantages of PBI carry through to the composite, while the processability of PEEK makes the products more functional.
Celazole® T-Series Value Proposition
The advantage of Celazole® T-Series over ordinary PEEK is the unexpected property set that results from the combination with PBI and other fillers (when present) that yield higher heat deflection temperatures (HDT), higher moduli, higher strength, improved wear resistance and lower creep. In the T-Series composites, HDT’s can be raised to 330ºC, just below the crystalline melting point of PEEK. The effect can be observed in the accompanying dynamic mechanical analysis (DMA) chart for TU-60 on this page.
A desirable balance of performance and tractability is obtained with the Celazole® T-Series products that place the group’s thermo-mechanical performance above PEEK, but below PBI. T-Series is designed for injection molding of parts that perform, but are cost effectively produced.
Celazole® T-Series Applications
Bearing cages
Bushings
Compressor vanes
Conveyor systems
Dynamic load bearing components
Dynamic seals
Electrical connectors
End effector pads
Gears
Glass handling
Metal spinning rollers
Office equipment
Oilfield equipment
Oven conveyors
Piston rings
Plane bearings
Planetary gears
Plasma torch tips, insulators, swirl baffles
Pump bearings
Semiconductor wafer transportation
Sliding surfaces
Soldering equipment
Synchronizer rings
Temperature sensor housings
Textile equipment
Thrust washers
Tilt pad bearings
Turbines
Turbo charger bushings
Valve seats, stem seals, packings
Celazole® T-Series TU-60 Typical Properties (PBI PEEK Compound)
Unreinforced Melt Processable PBI
Celazole® T-Series TU-60 is a high performance unfilled blend, ideal for applications requiring no fillers. This material works well for complex geometries and offers the best process ability. It is ideal for lamp sockets, connectors and backup seals.
MECHANICAL
Tensile Strength
--- Modulus
--- Elongation
Flexural Strength
--- Modulus
Compressive Strength
--- Modulus
THERMAL
Coefficient of Linear Thermal Expansion
--- 75‐300°F
--- 390‐570°F
Temperature of Initial (5%) Weight Loss In:
--- Air
--- Nitrogen
Celazole® T-Series TL-60 Typical Properties (PBI PEEK Compound)
Self Lubricating Melt Processable PBI
Celazole® T-Series TL-60 is a lube grade blend offering superior wear resistance, low friction, chemical resistance and high load bearing capability. It’s well suited for rotor vanes, thrust bearings, plane bearings, bushings and other friction management applications – particularly under load.
MECHANICAL
Tensile Strength
--- Modulus
--- Elongation
Flexural Strength
--- Modulus
Compressive Strength
--- Modulus
THERMAL
Coefficient of Linear Thermal Expansion
--- 75‐300°F
Heat Capacity @ 158°F
Heat Deflection Temperature
Temperature of Initial (5%) Weight Loss In:
--- Air
--- Nitrogen
Thermal Conductivity @ 70°F
Celazole® T-Series TF-60C Typical Properties (PBI PEEK Compound)
Carbon Fiber Reinforced Melt Processable PBI
Celazole® T-Series TF-60C is a carbon-reinforced blend, ideal for parts that require high strength, very low creep, and deflection resistance. A great match for planetary gears, office equipment, semiconductor, electronic and mechanical applications.
MECHANICAL
Tensile Strength
--- Modulus
--- Elongation
Flexural Strength
--- Modulus
Compressive Strength
--- Modulus
THERMAL
Coefficient of Linear Thermal Expansion
--- 75‐300°F
Heat Capacity @ 158°F
Heat Deflection Temperature @ 264 psi
Temperature of Initial (5%) Weight Loss In:
--- Air
--- Nitrogen
Thermal Conductivity @ 70°F
Celazole® T-Series TF-60V Typical Properties (PBI PEEK Compound)
Glass Fiber Reinforced Melt Processable PBI
Celazole® T-Series TF-60V is a glass-reinforced blend offering thermal and electrical insulation, wear resistance and dimensional stability with the cost efficiency of a direct form process. An excellent choice for high temperature electrical insulators, plasma torch drag cup shields, swirl baffles and parts requiring minimal thermal expansion.
MECHANICAL
Tensile Strength
--- Modulus
--- Elongation
Flexural Strength
--- Modulus
Compressive Strength
--- Modulus
THERMAL
Coefficient of Linear Thermal Expansion
--- 75‐300°F
Heat Capacity @ 158°F
Heat Deflection Temperature @ 264 psi
Temperature of Initial (5%) Weight Loss In:
--- Air
--- Nitrogen
Thermal Conductivity @ 70°F
Celazole® T-Series TK-60 Typical Properties (PBI PEKK Compound)
Unreinforced Melt Processable PBI/PEKK
Celazole® T-Series TK-60 is an unreinforced melt processable blend of PBI-PEKK (polyetherketoneketone).
MECHANICAL
Tensile Strength
--- Modulus
--- Elongation
Flexural Strength
--- Modulus
--- Elongation
Celazole® T-Series TKL-60 Typical Properties (PBI PEKK Compound)
Self Lubricating Melt Processable PBI/PEKK
Celazole® T-Series TKL-60 is a self-lubricating melt processable blend of PBI-PEKK (polyetherketoneketone).
MECHANICAL
Tensile Strength
--- Modulus
--- Elongation
Flexural Strength
--- Modulus
--- Elongation
Celazole® T-Series TK-60C Typical Properties (PBI PEKK Compound)
Carbon Fiber Reinforced Melt Processable PBI/PEKK
Celazole® T-Series TK-60C is a carbon fiber reinforced melt processable blend of PBI-PEKK (polyetherketoneketone).
MECHANICAL
Flexural Strength
--- Modulus
--- Elongation
Comparative Wear
In a thrust washer configuration wear test of competitive engineering plastics used in tribological applications, Celazole TL-60 proved itself an exceptional wear grade material. Over the range of 50 — 800 ft/min, TL-60 exhibited the lowest wear factors, the lowest coefficients of friction and the coolest counter-surface running temperatures in the group including wear grades of: polyetheretherketone (PEEK), polyamide-imide (PAI) and polyimide (PI).
Between 50 and 100,000 PV, the Wear Factors for wear grade PEEK were 4.6 times those of TL-60; wear grade PAI was 2.1 times higher; and wear grade PI 1.5 times higher than TL-60. The lower value (e.g. TL-60) is better, as a lower wear factor means less wear.
Because TL-60 is such a low friction material, it runs the coolest. That means longer part life. Between 50,000 and 100,000 PV across the full range of speeds, TL-60 ran nearly 100F cooler than wear grade PEEK; 50F cooler than wear grade PI; and more than 40F cooler than wear grade PAI. TL-60 is both strong and thermal resistant – making it the ideal choice for high load applications at moderate and low speeds. In the wear test, TL-60 was the only material to endure PV’s of 125,000 — 200,000 at the 50 ft/min speed and loads of 2500 — 4000 psi. The other materials failed by breaking or melting at these conditions.
Celazole® is a registered trademark is a registered trademark of PBI Performance Products, Inc.
We Provide Solutions
Regardless of the industry or end-use, we have the expertise to quickly and economically create the ideal polymer for the job.

Polymics,® Ltd. is the only polymers company in the world that has the expertise and manufacturing capabilities to take customers from high performance thermoplastic material development to final part molding and assembly. Our in-house polymers engineering staff provides our customers with true one-stop “Problem to Finished Part Solutions” by working on their individual problem from start to finish.
Celazole® is a registered trademark of PBI Performance Products, Inc.
QUICK LINKS
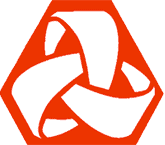
Corporate Headquarters
2215 High Tech Road,
State College, PA 16803
Tel: 814.357.5860
Fax: 814.357.5863
Email: info@polymics.com
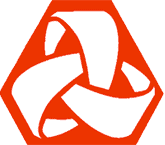
U.S. Sales Office
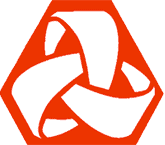
Asian Pacific
No.272, Huakang St.
Bade Dist., Taoyuan
Taiwan, 33464
Tel: 886.3.377.0518
Fax: 886.3.367.2115
Email: info@polymics.com
This information and all further technical advice are based Polymics’ present knowledge and experience. However, neither Polymics Ltd nor any of its affiliates makes any warranty, express or implied, including merchantability or fitness for use, or accepts any liability in connection with this information or its use. This information is for use by technically skilled persons at their own discretion and risk and does not relate to the use of this product in combination with any other substance or any other process. This is not a license under any patent or other proprietary right. The use of this product resides on the determination of the customer not Polymics Ltd. The customer must determine suitability of any information or material for any contemplated use, the manner of use and whether any patents are infringed. This information gives typical properties only and is not to be used for specification purposes. Polymics reserves the right to make additions, deletions, or modifications to the information at any time without prior notification.