Processing & Forming
Injection Molded Tubes
Polymics,® Ltd. offers “two-shot” injection molding, insert and overmolding, and other injection molding processes in order to provide the best solution in the shortest amount of time by eliminating the need for any final annealing or machining processes.
Injection molded tubes can be made up to OD 15.0″ in 0.25″ increments with wall thicknesses up to 0.75.” Tubes are available in 6.0″ lengths.
Standard Injection Molded Tube Materials
Please note that while the materials shown below are the standard commercial materials offered by Polymics, Ltd., Polymics has the experience and capability to compound custom shapes from a wider range of thermoplastic resins and fillers. Please contact us with any questions or inquiries you may have for materials not shown here.
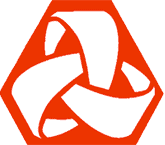
PEEK
Unfilled, 30% Glass Fiber, 30% Carbon Fiber, Wear Package, and 15% PTFE-Filled Polyetheretherketone
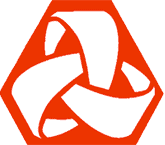
PPS
Unfilled and 40% Glass Fiber Polyphenylene Sulfide
Fabricated Parts
Polymics,® Ltd. is able to combine machining processes to give you a complete solution that has been tailored to your application. All of our finished parts are completed to customer requirements and can be made from customer-provided drawings.
If your existing parts are not working, Polymics,® Ltd. is ready to help you upgrade to a better solution by replacing the material or providing you with a better-fitting component.
Compression Molded Shapes
Hot Compression Molded shapes manufactured by Polymics,® Ltd. provide engineers and machinists with the quality and performance required for the most demanding applications. Polymics,® Ltd. is currently Compression Molding Plates, Rods, Tubes, Discs, and Near Net Shapes.
Compression Molding is among the most economical of options because it offers a wide range of near net sizes and produces materials with low minimum order quantities. As a result, users can buy exactly the amount of material needed without having to pay additional charges for tooling or small run set-ups.
Benefits of Compression Molding
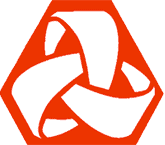
Lowest cost to create molds
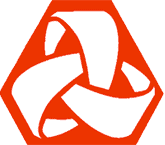
Minimal waste
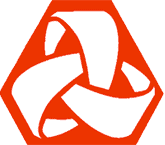
Reduced labor costs
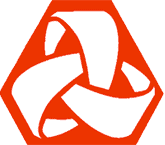
Minimization of final internal stress and warping
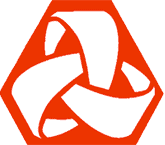
Stability & Accuracy
Standard Thermoplastic Sizes/Shapes
Plates
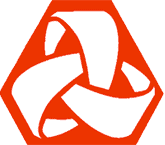
12.0" x 6.0"
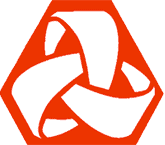
Thicknesses from 0.25" to 1.5"
Rods
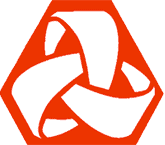
Diameters from 2.0" to 4.0"
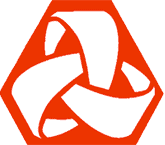
Lengths from 0.25" to 3.0"
Discs
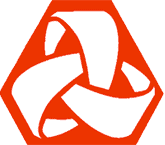
Outer Diameters (OD) from 2.0" to 5.0"
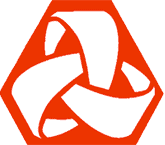
Wall Thicknesses up to 2.0"
Tubes
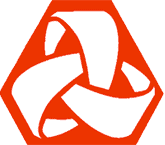
Outer Diameters (OD) from 3.0" to 5.0" in Lengths of 3.0" with Wall Thicknesses up to 1.75"
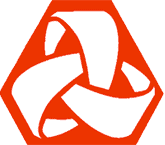
Outer Diameter (OD) of 10.25" in Lengths from 0.5" to 1.1" with Wall Thicknesses up to 2.6"
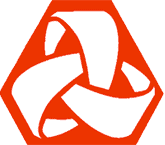
Outer Diameter (OD) of 15.125" in Lengths from 0.5" to 1.0" with a Wall Thickness of 0.5"
Standard Materials
Please note that while the materials shown below are the standard commercial materials offered by Polymics,® Ltd., Polymics,® Ltd. has the experience and capability to compound custom shapes from a wider range of thermoplastic resins and fillers. Please contact us with any questions or inquiries you may have for materials not shown here.
Polyketones (PEEK, PEKK)
Polyimides (PBI, PI, PEI)
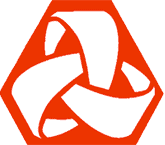
Pyramid™ PEEK
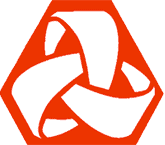
Pyramid™ CC PEEK
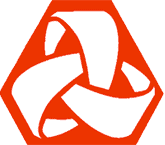
Arylmax® PEKK
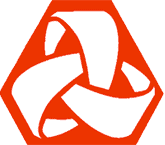
Celazole® PBI
Unfilled, Carbon-Filled, Electro-Static Dissipative (ESD), Easy Machinable, and T-Series PEEK/PBI Blends
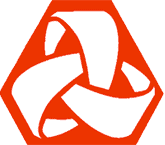
Pyramid™ PI
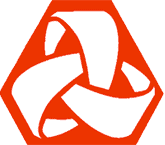
Ultem® PEI
Other Standard Materials (PPS, PPSU, PBT, PSU)
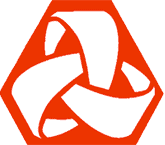
Pyramid™ PPS
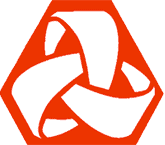
Pyramid™ PPSU
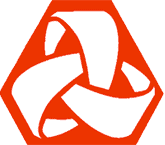
Valox® PBT
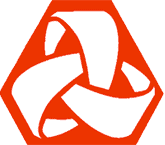
PSU
We Provide Solutions
Regardless of the industry or end-use, we have the expertise to quickly and economically create the ideal polymer for the job.

Polymics,® Ltd. is the only polymers company in the world that has the expertise and manufacturing capabilities to take customers from high performance thermoplastic material development to final part molding and assembly. Our in-house polymers engineering staff provides our customers with true one-stop “Problem to Finished Part Solutions” by working on their individual problem from start to finish.
Celazole® is a registered trademark of PBI Performance Products, Inc.
QUICK LINKS
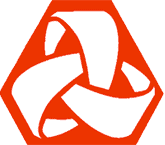
Corporate Headquarters
2215 High Tech Road,
State College, PA 16803
Tel: 814.357.5860
Fax: 814.357.5863
Email: info@polymics.com
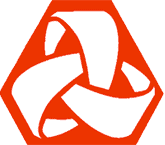
U.S. Sales Office
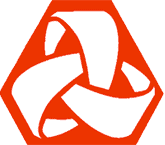
Asian Pacific
No.272, Huakang St.
Bade Dist., Taoyuan
Taiwan, 33464
Tel: 886.3.377.0518
Fax: 886.3.367.2115
Email: info@polymics.com
This information and all further technical advice are based Polymics’ present knowledge and experience. However, neither Polymics Ltd nor any of its affiliates makes any warranty, express or implied, including merchantability or fitness for use, or accepts any liability in connection with this information or its use. This information is for use by technically skilled persons at their own discretion and risk and does not relate to the use of this product in combination with any other substance or any other process. This is not a license under any patent or other proprietary right. The use of this product resides on the determination of the customer not Polymics Ltd. The customer must determine suitability of any information or material for any contemplated use, the manner of use and whether any patents are infringed. This information gives typical properties only and is not to be used for specification purposes. Polymics reserves the right to make additions, deletions, or modifications to the information at any time without prior notification.